Collaboration reduces energy consumption by a factor of 10: "This means a huge increase in production capacity"
A research project used artificial intelligence to help the SME C.C. Jensen to reduce energy consumption on drying oil filters by a factor of 10, and to reduce production time significantly.
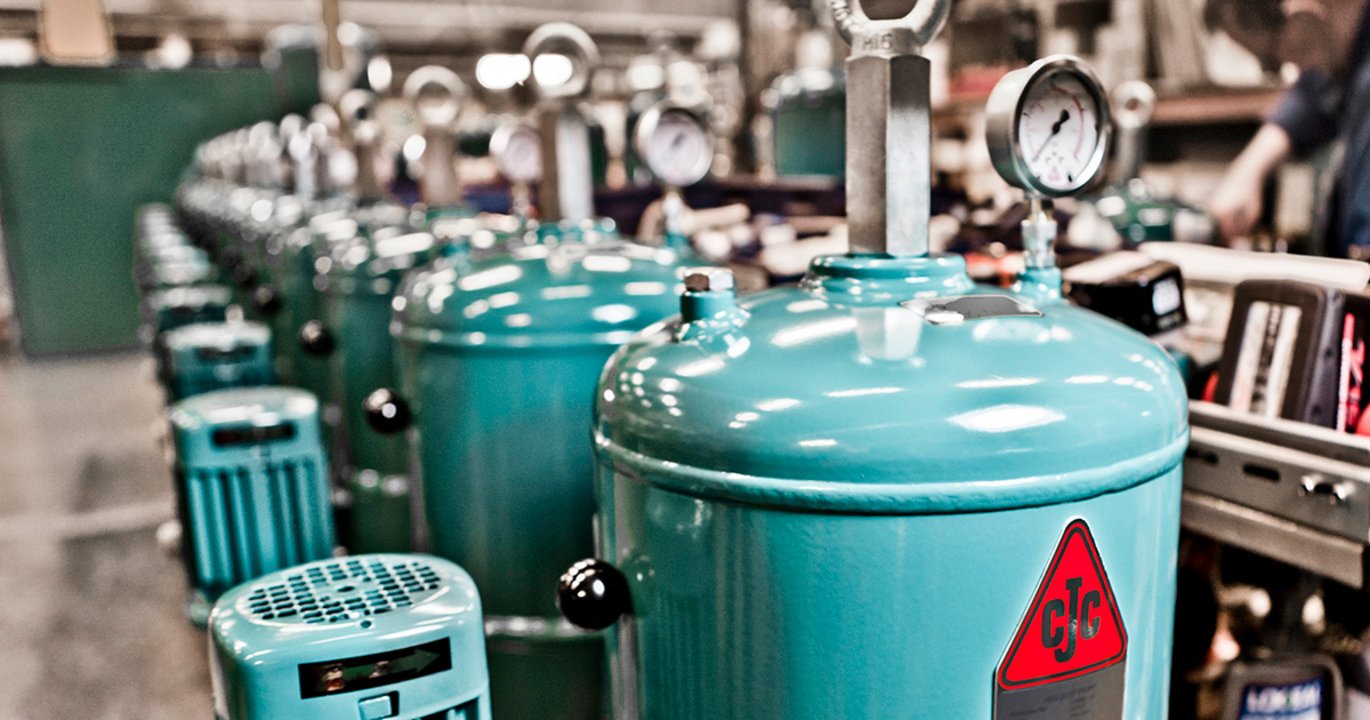
"When can we turn off the oven?"
This has been a big question for the company C.C. Jensen, which produces oil filters to make sure that systems like a ship's engine run smoothly and give a signal when maintenance is required.
The oil filters should not be too dry or too wet, they have to have just the right level of dryness to make for better quality and uniformity, and to make the production time shorter.
In a MADE FAST research project with Aarhus University, C.C. Jensen found the answer by coupling sensors to their systems and letting artificial intelligence (AI) predict when the level of dryness is just right, so that they do not use unnecessary energy to heat furnaces.
"We’ve done a lot of drying experiments with Machine Learning to train a computer model to assess when it is dry. It’s simply a neural network," explains Jens Fich, technical director at C.C. Jensen.
Because the filters consist of natural fibres, they do not dry equally quickly, so there was a need for a new solution. It could have been possible to use a very complex package of sensors to measure air humidity, but C.C. Jensen went in another direction.
Stronger competitiveness
"The MADE project helped us develop this AI model, and it’s an important piece of a bigger jigsaw puzzle: It’s helped to reduce our energy consumption for the drying process by a factor of 10. We’ve also achieved an increased production rate. 37 per cent less drying time per filter on average. This means a huge increase in production capacity," says Jens Fich.
At Aarhus University, Professor Peter Gorm Larsen, head of DIGIT (Centre for Digitalisation, Big Data and Data Analysis) and co-supervisor on the PhD project, is pleasantly surprised by the results.
"It's fantastic. I never imagined that it would be possible to reduce energy consumption by a factor of 10. C.C. Jensen probably approached drying with belt and braces previously. They wanted to ensure that their filters always meet a very high standard. Quality is what we live on in Denmark. It’s clear that they also save time if they only a need to have the ovens turned on for a tenth of the time," he says.
Part of the explanation is that C.C. Jensen's drying process at the factory in Hesselager was its most energy-intensive process. At the same time as implementation of the AI model, the filter manufacturer converted from using wood pellets to generating electricity with heat pumps that are now the source of heat to dry the filters.
"The results are impressive - and I'm delighted to see that through research we can strengthen competitiveness. The techniques can inspire other production companies to optimise their energy consumption," says Nigel Edmondson, the director of MADE.
The imperfect is useful
When working with machine learning, it is important to be aware that errors will occur from time to time, says Peter Gorm Larsen.
"The potential for machine learning is huge, provided it isn’t absolutely necessary for the model to respond correctly 100 percent of the time. An AI model will never be perfect, but it is useful when it’s better at the work than people – in other words, simply making fewer errors. In this case, the computer is better at predicting than the human eye. In a drying process, 95 – 99 per cent is enough to improve the process, but of course this doesn’t apply if AI is to control autonomous cars in the middle of a city," he says.
There are no guarantees that machine learning will work, but there is a good chance of this, if a production company has regular data.
"It works because we’ve analysed which tools work here. It’s a bit like trying out different tools from a toolbox: A screwdriver is not as good at knocking nails into the wall as a hammer. This is how you build up knowledge," continues Peter Gorm Larsen.
C.C. Jensen has been keen to get precisely this research knowledge out to the entire organisation, and this work was made easier when Aarhus University employed MADE PhD Christian Remi Wever from C.C. Jensen.
"It's been a huge advantage to have one of our own affiliated as a PhD. This has meant that we’ve been able to easily integrate new knowledge from the project into our organisation. We’ve now implemented the AI solution on a trial basis, so it’s not yet fully implemented, but we can see that it works," says Jens Fich, technical director at C.C. Jensen.
"There’s money to be made"
The research project is nearing completion, and it is important to ensure that the results are disseminated widely, so that the new knowledge can benefit other manufacturing companies. Machine learning can come into play in many other processes where there is a need for predictions:
"There’s money to be made in areas of production where you want to ensure the right quality in 99 per cent of cases. If companies can get their data out and get help from knowledge institutions that know which tool to use now, they can produce strong results that save energy. This is good for the green transition," says Peter Gorm Larsen.
This article is a reproduction of this article published on made.dk.
About the project
Title: Improving Filter Insert Performance and Quality using Simulation and Data Analytics
The project is part of the MADE research platform under the 'Digitisation of production processes' initiative.
Partners: C.C. Jensen, Universal Robots, Aarhus University, DTU, Danish Technological Institute and FORCE Technology
Period: From March 2021 to February 2024
Innovation Fund Denmark is the largest single investor with DKK 79.8 million. The total project budget in MADE FAST is DKK 265 million.
About MADE:
MADE – Manufacturing Academy of Denmark – is Denmark's production cluster. MADE consists of companies, universities, GTS institutes and educational institutions. MADE creates and supports world-class Danish production. As a cluster, MADE gathers together the ecosystem around Danish production via conferences, company visits, open labs and projects.
Contact
Professor Peter Gorm Larsen
Department of Electrical and Computer Engineering
Email: pgl@eng.au.dk
Tel.: +45 41893260